3D printing and its applications
Aerospace and Defense Industry:
Automotive Industry:
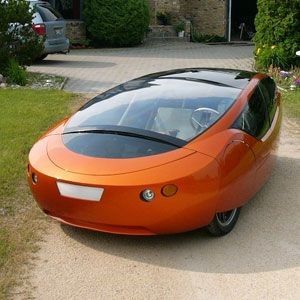
Medical & Dental Industry
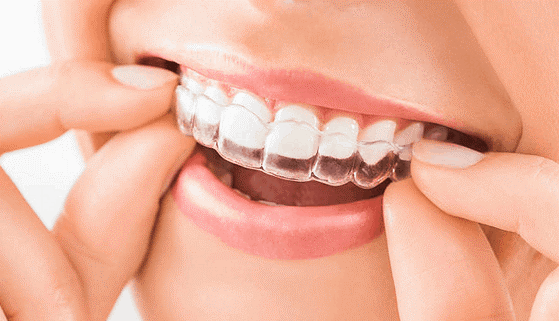
The fastest-growing adopters of 3D Printing is the medical and dental industry. The professionals in this field believe that this technology will continue to innovate and transform the face of dentistry. The applications of additive manufacturing for the medical industry are versatile and wide-ranging- from medical devices to prosthetics and even bioprinting!
The benefit of 3D printing in the Medical and Dental Industry is that it can provide personalised patient care, cost effectively. One can create customised and complex designs of medical devices. Medical device manufacturers can produce faster and efficiently with the help of 3D printing technology. The medical industry can leverage the capabilities of 3D printing to create patient-specific devices. For example, devices such as prosthetics and implants can be produced faster and more affordably than with traditional manufacturing methods.
Clear aligners & digital dentistry:
3D Printed clear aligner moulds are used to produce the majority of these aligners. The key reason for using 3D printing in manufacturing clear aligners is the ability to customise them cost-effectively, since clear aligners are inherently individualised products.
By combining intraoral scanning and 3D printing, dental labs can create dental products like crowns, bridges and bite splints that perfectly match a patient’s anatomy. Surgical tools and guides can be produced faster at lower-costs using this technology.
Implants & Prosthetics
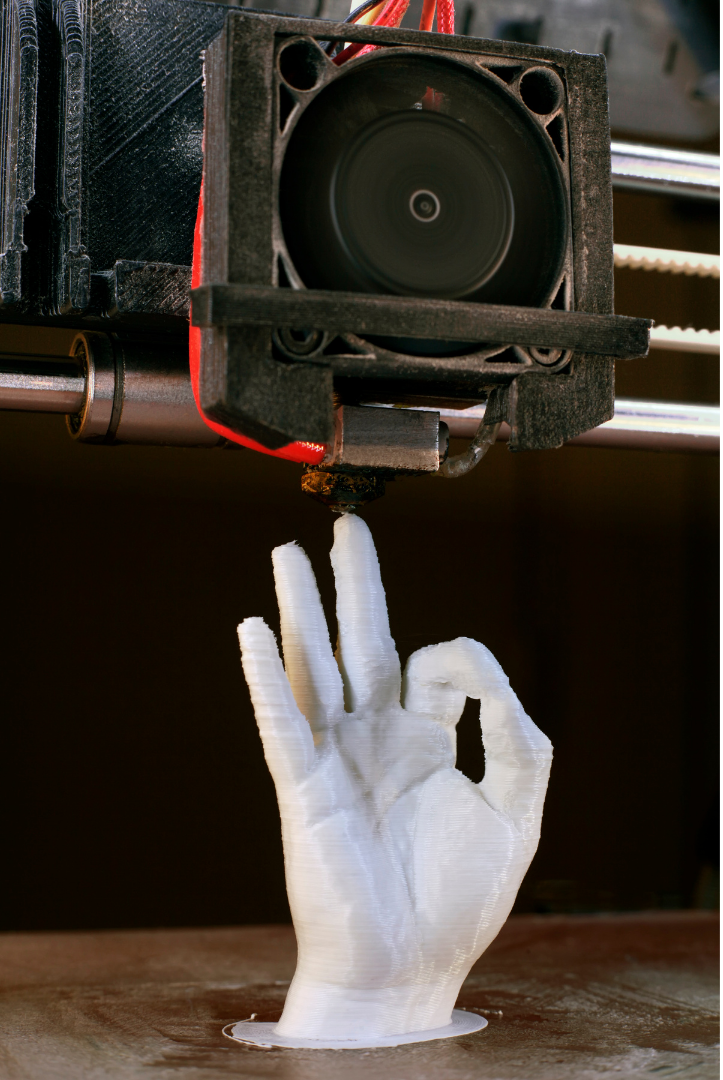
Certified biocompatible plastic or metal (e.g. titanium) materials is used to create custom prosthetics and orthopaedic devices using the 3D Printing technology.
When it comes to implants, 3D printing is currently being used to create hip and knee joint replacements, cranial reconstruction implants and spinal implants.
In one example, a mountaineer needing a hip replacement, received Lima Corporate’s hip implant featuring a 3D-printed acetabular cup. Thanks to 3D printing, it was possible to produce a cup that mimics the porous structure of natural bone, improving osseointegration, a process which allows an implant to become a permanent part of the body.
Ultimately, the patient was able to walk and climb again just after two and a half months after the implantation.